Design for Manufacturability: Optimizing Product Development for Efficient Production
Table Of Content
- What Is the Process of Designing a Product for Manufacturing?
- How Does DFM Differ From Traditional Product Design Methods?
- How do you deal with sharp corners in CNC machining? Designing with the machinist in mind
- Easier to scale up production
- Key DFM Principles for Product Design
- Assembly with DFM Principals
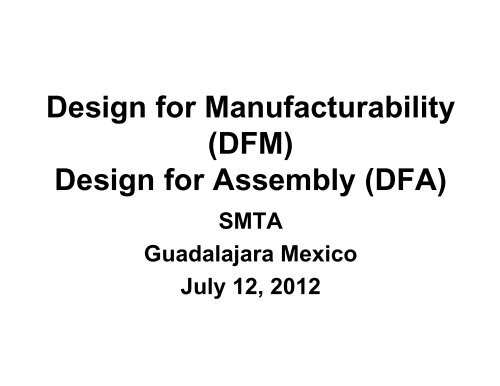
Optimizing designs for efficient manufacturing enables companies to stay competitive in a rapidly evolving market. Efficient designs result in reduced material waste and energy consumption during manufacturing. DFM aligns with sustainable practices, contributing to a more environmentally friendly approach to product development. With a large number of manufacturing processes and complex cost drivers, DFM product modeling has, historically, been a serious analytical challenge. Today, digital manufacturing simulation tools are enabling engineering organizations to institute deep DFM modeling that would have been computationally prohibitive in the past. There are several factors to take into consideration when designing for manufacturability.
What Is the Process of Designing a Product for Manufacturing?
Supply Chain Fundamentals: Manufacturing - Techstars
Supply Chain Fundamentals: Manufacturing.
Posted: Tue, 28 Jul 2020 07:00:00 GMT [source]
Specially designed AI software can enable visualization of manufacturing and assembly processes, so potential issues may be avoided. Collaboration between humans and machines makes for the highest level of insight and accuracy. The DFM process reduces costs, lowers lead times and improves the quality of custom parts. Design for Manufacturability plays a pivotal role in modern product development. By considering manufacturing processes from the outset, businesses can create products that are not only innovative but also efficient to produce. Emphasizing collaboration, simplicity, and continuous improvement, DFM sets the stage for more cost-effective, high-quality, and sustainable products.
How Does DFM Differ From Traditional Product Design Methods?
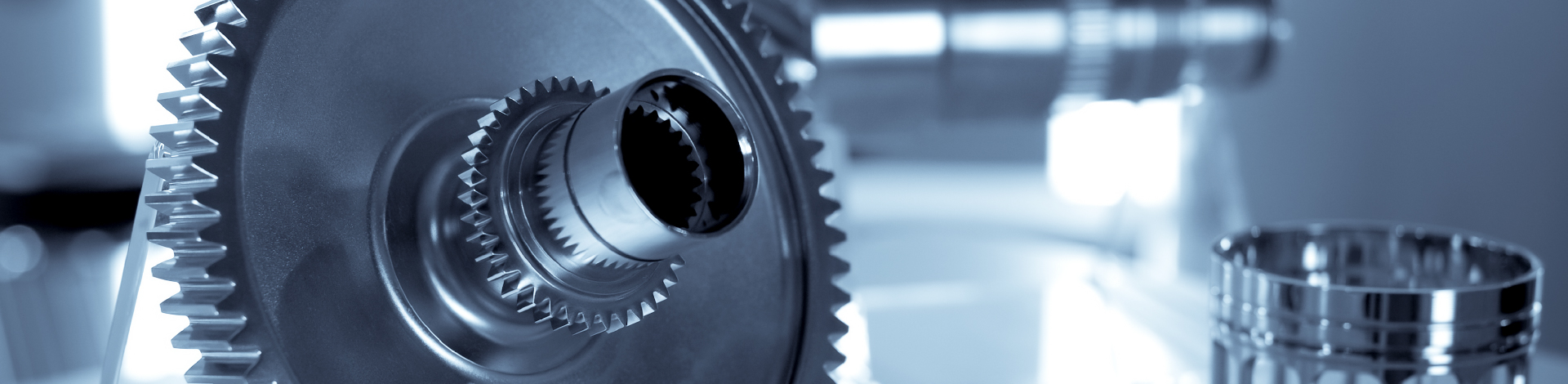
How can you create a part or product that’s ready to move from prototype to production? Check out our article, which offers tips and tricks for designing with scalability in mind. Design for manufacturing (DFM) means taking a design-first approach to manufacturing.
How do you deal with sharp corners in CNC machining? Designing with the machinist in mind
Identification of potential manufacturability issues should be highly graphical and pinpoint areas for improvement. For example, the system should be able to quickly identify any machining operations where the cycle time is abnormally high. While there may be a good reason for this, it may also identify a design flaw that, if corrected, could dramatically accelerate the manufacturing process and drive down cost accordingly.
Strategies for Implementing DFM
How digital manufacturing supported an award-winning wheelchair - Med-Tech Innovation
How digital manufacturing supported an award-winning wheelchair.
Posted: Wed, 02 Aug 2023 07:00:00 GMT [source]
This approach often focuses on principles like minimizing the total number of parts used, ensuring that parts are easily insertable, and confining assembly requirements to simple, repetitive motions. In these cases, customers often spend valuable time and money on revisions and extensive back-and-forth communication with their manufacturing partner. Your parts may need to adhere to industry-specific, internal and/or third-party standards. If your components will be used in an environment in which food is present, for example, your product must comply with all food-safe standards and regulations. Consider all standards, and plan for testing to ensure that these standards are met, during the DFM process. In the era of heightened environmental consciousness, the integration of sustainable and eco-friendly design practices within Design for Manufacturability (DFM) has gained significant importance.
Easier to scale up production
It can be helpful to distinguish design for manufacturability from the closely related idea of a design for assembly. Manufacturability describes the degree to which a product can be effectively manufactured given its design, cost, and distribution requirements. To create a design that can be inspected using a functional gauge, you must design for Maximum Material Condition (MMC). A feature is at maximum material condition when it contains the largest amount of material allowed by its size tolerance.
Analyze the Material
Design for manufacturing (DFM) is important because it can save manufacturing costs and complexity by a large margin while maintaining good product quality. Businesses may reduce material waste, improve production procedures, and boost overall efficiency by designing with ease of manufacture in mind. In addition to lowering costs, this strategy promotes a quicker time to market and increased industry competitiveness.
Key DFM Principles for Product Design
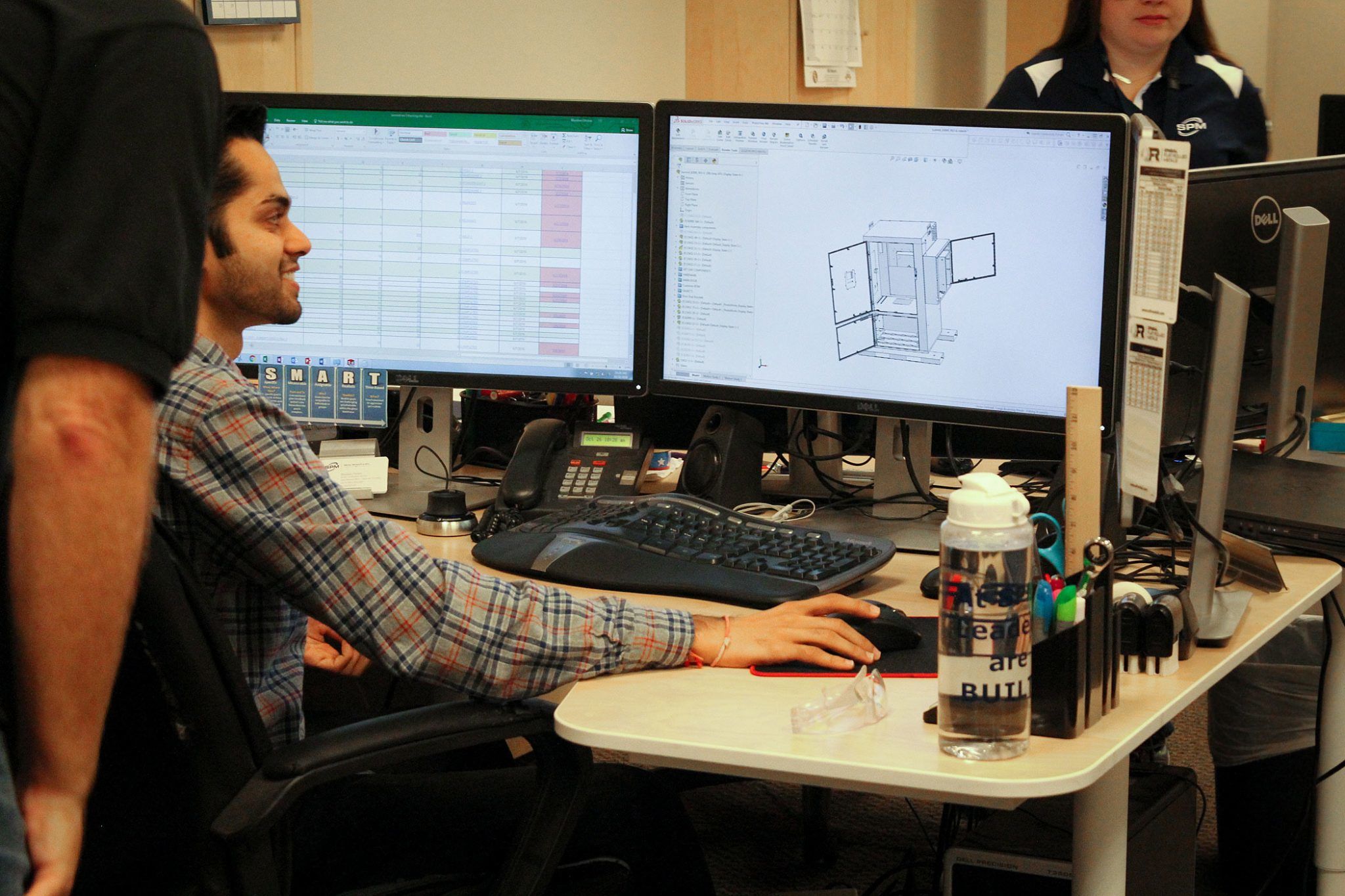
For instance, reducing the total number of parts in the assembly and designing out fasteners will speed up the assembly process significantly and increase the overall efficiency. Another key factor to avoid problems down the line is to reduce the probability of incorrect assembly by carefully designing individual components so that they can only fit in a specific orientation (mistake-proofing). When designing a part for manufacturability, everyone who has a stake in the product should be involved. Some other departments involved with the product include Quality (inspection), Purchasing (material procurement), and even Marketing. The vendors from which you would be buying materials and components should also be consulted. Having all stake-holders involved during the design process will help potential problem areas come to light earlier in the process.
A willingness to re-think a product from the ground-up is an essential element for generating the most impactful estimate. To generate manufacturing analyses during the design stage, your software must be extremely fast and very easy to use. With aPriori, the modeling process begins by analyzing a 3D CAD model to generate a digital twin. Rafael, an Israeli aerospace company, uses aPriori as their enterprise digital manufacturing simulation software including DFM analyses.
DFM is applied during the design phase to ensure the product is straightforward, reducing manufacturing costs and complexity. DFM principles often emphasize standardization and modular design, which facilitate using standard components across multiple products. This approach simplifies inventory management and reduces the complexity of the supply chain. Suppliers benefit from producing standardized components, leading to cost savings through economies of scale.
Designers and manufacturers combine their unique expertise to identify solutions that reduce costs and lead times. While it might be tempting to specify tight tolerances across the board to ensure high-quality products, it can drastically increase costs. Use tolerances as loose as possible while still meeting functional requirements to facilitate more accessible, more cost-effective manufacturing. Every recommended change should undergo a cost-benefit analysis to determine its viability.
Tolerance analysis ensures that parts fit together correctly, even if not manufactured perfectly. When plans are aligned with manufacturing capabilities, fewer design iterations are required during the production phase. This streamlined approach accelerates the production ramp-up, allowing companies to introduce new products to the market faster, capitalizing on competitive opportunities and capturing consumer demand. The mid-20th century marked a significant shift in manufacturing as industries geared up for war efforts. Mass production techniques became more refined, but complexity increased due to the demands of advanced weaponry. Post-war, manufacturers sought ways to streamline production while maintaining quality and minimizing costs, giving rise to the foundation of modern DFM principles.
Doing so will make manufacture less time-consuming, which will reduce cost and increase ease of manufacturing. The exact process of DFM will depend on what product is being designed and produced. Other basics of effective DFM include standardisation of parts to save on part cost, design simplicity, which may reduce the complication or number of parts required, and setup time reduction. By designing products with manufacturing efficiency in mind, companies can minimize complexities in assembly, reduce the need for specialized tooling, and optimize production layouts. Simplified designs lead to faster manufacturing processes, lower labor costs, and decreased waste, contributing to overall cost savings. By simplifying and optimizing the product design, DFM aims to achieve better manufacturability, leading to improved overall product performance and competitiveness in the market.
By following these best practices, your organization can optimize designs for easier, more efficient, and cost-effective manufacturing, thus realizing DFM's full benefits. Creating internal DFM guidelines and checklists can be a practical way to help designers consider manufacturability aspects systematically. These should be easy to follow and cover significant points of concern, such as materials, part count, assembly considerations, and process capabilities.
Fractory’s bending calculator helps you to get your sheet metal designs right from the start. For example, if you understand the writer's intent, it's much easier to make the corrections in the text. But if you're reading the essay without a clear understanding of intent, you might go back and forth with corrections before you come up with a finished copy. Managing tolerances is an essential part of a good DFM, and there should always be a justification for the numbers on the drawing.
Apple's design principles for manufacturability epitomize the intersection of innovation and efficient production. Renowned for their sleek, functional products, Apple's approach to DFM combines aesthetics with practicality. Any issues can be addressed in the plan before production, avoiding costly modifications to tooling and processes. Manufacturers often achieve significant cost savings by relaxing tolerances without affecting product quality.
Comments
Post a Comment